We are fans of Slice engineering and are impressed by their new products. We had tested and reviewed their mosquito last year. Now they recently launched a new hot end that is awesome and a bit more affordable.
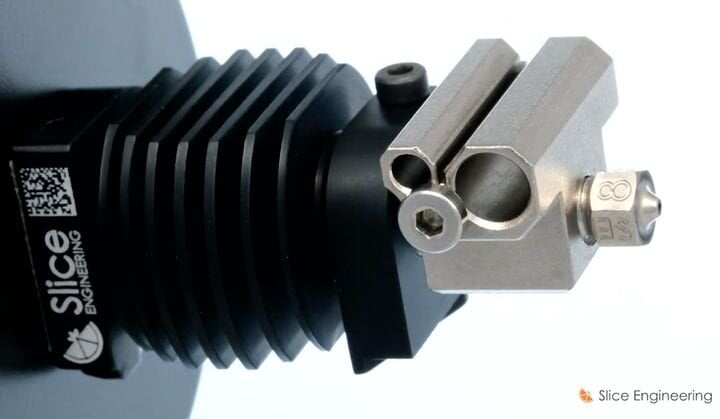
The Copperhead is designed by Slice Engineering, a Florida-based firm that previously introduced the Mosquito hot end, a 450C device that featured a “one handed change” capability. Now they’ve come up with an improved hot end they call the Copperhead.
There’s a good reason for calling it the Copperhead, as it is made from a great deal of copper. As you can see in this diagram, they use a bimetallic structure involving copper, aluminum and steel elements.
They’re attempting to increase the effectiveness of the heatbreak. This is the component that separates the cold and hot zones within the device, and it is critical to correct extrusion.
The reason has to do with the contradiction required within the “hot end”. One segment must heat up and soften the filament suitable for extrusion, but the other end must maintain a colder temperature so that the filament remains rigid and able to be pushed into the hot zone.
3D Printer Heatbreak Problems
Today’s hot ends generally do this quite well. If they don’t, then the filament becomes soft where it should not and extrusion problems result. Usually this is a stripped filament, as the gears gripping the filament simply pull off chunks of soft material rather than pushing the filament.
But there’s another effect that’s been happening in 3D printing these days: high temperature 3D printing. This is a result of increased interest in the use of engineering materials such as PEEK or ULTEM.
These high temperature materials require, obviously, higher extrusion temperatures. But that means the hot zone is hotter, and the cold zone must somehow remain cold despite being attached to a much hotter hot zone.
If inefficient, the higher heat could leak upwards into the cold zone and cause issues and ultimately filament jams. This is particularly evident on long duration 3D print jobs, where there is a lot more time for that heat to seep into the cold zone.
The Copperhead Hot End
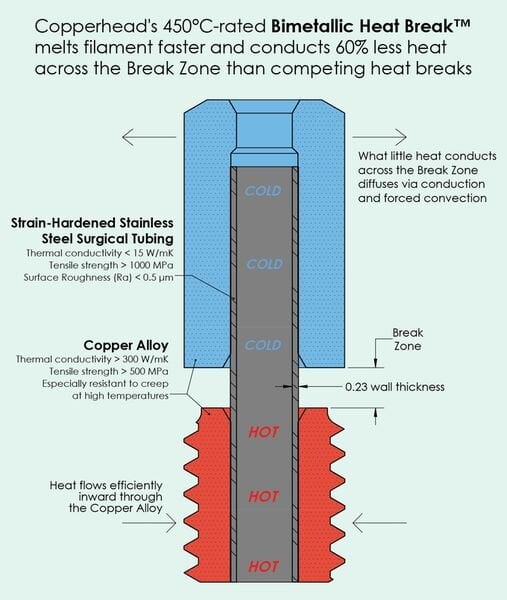
Enter the Copperhead. It is specifically designed to maintain the two separate thermal zones with the use of copper. That metal has excellent thermal transfer properties, and their design seems to leverage that very well.
Slice Engineering claims the Copperhead “conducts 60% less heat” across the heat break, and they’ve been able to verify this by using a thermal camera to observe the flow of heat, as seen here:
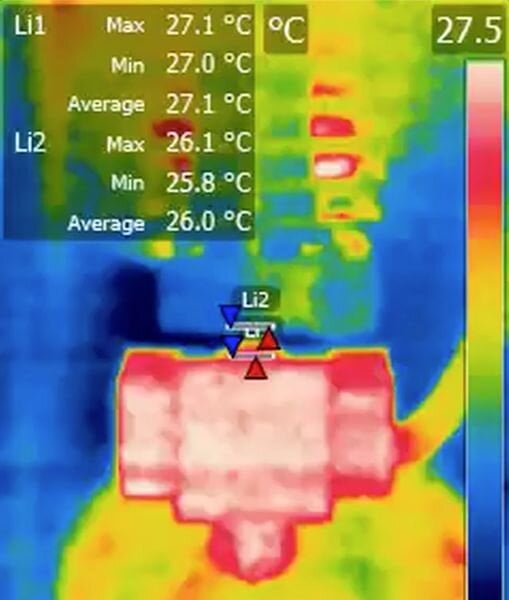
Mounting The Copperhead Hot End
The Copperhead is designed to be easily mounted on many different 3D printer platforms and systems. They explain:
“There are a few variants of the Copperhead™ (please see the Copperhead™ Variants table on the main campaign page), but three main mounting methods:
1. Groove mount – this is a standard groove style adapter common on many 3D printers. It includes a fitting to retain a PTFE tube
2. Heat break clamp – the “Standard” and “Mk10” variants of the Copperhead™ have straight shanks which can be clamped onto with a shaft collar or held in place with a set screw
3. Threading – the “RepRap 1.75”, “RepRap 2.85” and “Mk 8” versions of the Copperhead™ thread directly into a heat sink or base plate on the OEM extruder or carriage/end effector.”
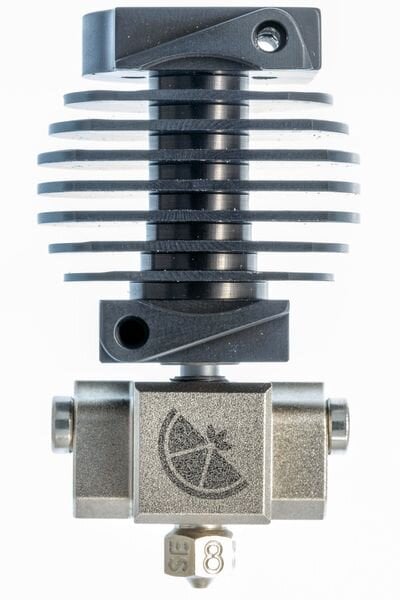
We are going to order one of their hotends soon to test and review on our Lotmaxx SC-10 or the JGMaker A5S or one of the future printers that we are reviewing and beta testing soon.
Please click here to check out more information from Slice Engineering’s website https://www.sliceengineering.com/products/copperhead%E2%84%A2